Outdoor Bathroom Pods are a valuable construction solution for multifamily apartment projects. They can save project teams time and money while providing a higher level of quality than traditional bathrooms.
Tight design and manufacturing processes in an offsite environment mean fewer defects. Streamlined installation reduces waste levels and makes for a cleaner job site.
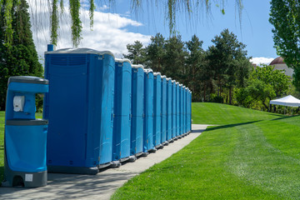
Bathroom pods are designed, built, and quality-approved in a controlled factory environment, which is far more efficient than traditional construction on site. For example, prefabricated wall and floor panels can be machined in the factory, ensuring that the design is fully adhered to and that each panel is a precise fit, saving time on site. Similarly, the production process is more predictable and streamlined so that trades can work with greater precision on tasks such as electrical installations, tiling and sealant application, something that is difficult to control on site.
A modular approach also provides the opportunity to reduce the number of different suppliers required on a project, delivering cost savings. For instance, a conventional construction would typically require multiple different bathroom products from a range of manufacturers and multiple subcontractors such as plumbers, electricians, glaziers, tilers, interior designers and carpenters. This is not only inefficient but can lead to disputes and delays on a project.
With bathroom pods, the manufacture and construction is completed by a single supplier, removing the need to coordinate and manage multiple supply chains. This streamlined process also allows each pod to be fully tested and quality-approved prior to shipping, which reduces the risk of defects on site.
Increasingly, manufacturers of pods are designing each design to be fast and simple to install on site, for example, with mechanically-fitted pan connectors and pre-wired junction boxes to simplify plumbing and electrics. This efficiency enables the bathroom to be offloaded, lifted, and installed on the floor in just hours – significantly faster than it can be constructed on site and reducing the need for additional storage on site. This translates into a faster return on investment for the developer or early occupation for the client, as well as reduced snagging and the assurance of completion on time and within budget.
Bathroom pods are manufactured in a controlled offsite environment, meaning they can be produced in parallel with on-site construction and installed quickly, reducing overall project timelines. They also allow for tight quality control and consistency, which reduces the risk of problems on site. This can be a significant benefit on complex projects where multiple trade professionals are working in limited space and constructing precise finishes.
When choosing a manufacturer to supply pods, ensure they have a good track record and financial stability. A visit to their factory can also be beneficial, as it allows you to inspect the manufacturing process and see if they can meet your specifications. The company should also be able to demonstrate their expertise in design and construction.
Another factor in shortened construction times is that bathroom pods are completed offsite, so there is no need for tradespeople to travel back and forth to site with building materials. This helps to keep onsite disruption and noise levels low, creating a safer and more efficient work environment.
The design of bathroom pods also makes them more energy-efficient. In addition, the manufacturing process of these prefabricated units uses fewer raw materials than traditional onsite construction, which results in a lower carbon footprint. This is ideal for construction projects that are focused on sustainability and green building certifications.
Finally, prefabricated bathroom pods require less storage space, as they can be delivered to a construction site fully completed. This means there is no need for builders to find additional storage space or create a bespoke storage solution on a busy construction site. The reduced program saved through the use of pods can result in faster returns for developers or early occupation for clients.
Pods can be designed and built in a range of sizes and dimensions to meet different project requirements. As they’re prefabricated in a controlled factory environment, the quality and standards remain consistent from one unit to another – making them an ideal construction method for complex or multiple occupancy developments such as hotels, schools, hospitals, or student accommodation.
Using bathroom pods also provides significant flexibility on a construction site. As a result, the overall construction programme can be reduced significantly and completed to an earlier date. This helps reduce construction loan interest and enables tenants to move in sooner, giving a better return on investment for developers.
The use of bathroom pods also eliminates a large number of work at heights and reduces the amount of heavy materials that need to be transported around the construction site. This reduces risks for workers, improving safety and reducing the number of accidents that occur on site.
Another advantage of bathroom pods is that they can be designed and manufactured to include domestic water piping, electrical components, lighting, and GFCI (ground-fault circuit interrupter) whips that are ready for connection. This means that installers don’t have to spend time laying out and cabling these connections on site, which helps improve productivity.
Achieving this level of flexibility does require some upfront planning and an early design freeze so that the bathroom pod manufacturer can order all of the components and start manufacturing. However, the payback in terms of increased productivity on site and a quicker completion schedule will more than offset this initial hard cost.
Pods are built with light gauge steel framing for superior strength and accuracy, as well as moisture-resistant wallboard that ensures the unit will last. They’re also delivered fully finished to the job site, meaning you don’t have to pay extra for installation, labour and materials like with traditional on-site construction. These savings add up over the course of your project, helping you save money and stay within budget.
Bathroom Pods are also made offsite, which means you eliminate the need to coordinate several subcontract trades at the same time. This reduces the amount of labour, supervision and equipment requirements on-site – as well as cutting down on materials wastage and storage costs.
Another advantage of using pods is that they’re often built to higher quality standards than those constructed on-site, which helps you achieve better results for your clients and minimize any defects in use. For example, the tiling is typically set in such a way that it won’t come loose over time, and the caulking joints have a smooth finish.
Although bathroom pods offer many benefits, they do require some planning and coordination to get right. This includes early design freeze to ensure the pods are designed to fit seamlessly into your building and are manufactured efficiently, as well as careful sequencing of the site works to avoid clashes. Using pods can also have a commercial impact on your project’s cash flow, as the upfront procurement of high-cost fitting-out materials is essential. However, the long-term cost benefits of using pods far outweigh this initial investment.
Bathroom pods are designed and built in accordance with project-specific requirements and dimensions. They can be used in a wide range of buildings, from student accommodation to military housing. The design of the pods is adapted for each use and a full range of plumbing, electrical and other services can be fitted. Unlike site-based construction, there is often only one pod supplier for all the products and materials that need to be delivered to site, simplifying procurement and mitigating delays caused by multiple suppliers bringing in different materials.
The production line environment of offsite manufacture can also offer consistency and improved productivity, while the repetitive nature of pod production makes it much easier to achieve consistent quality standards than on site. Pre-delivery testing in the factory should be stringent, with any defects rectified and remedied prior to installation, to minimize the risk of any on-site issues.
With offsite production, the waste produced on a construction site can be reduced. This is because the factory uses lean processes that optimize the use of materials and eliminates waste. There are also strict environmental regulations in place that ensure a high level of sustainability and compliance.
Increasing demand for quick and efficient construction solutions during the pandemic drove growth in the global prefabricated bathroom pods market. This was due to the urgent need to build hospitals and isolation facilities, which were unable to be constructed in time using traditional methods.
As the market continues to recover, we are seeing more developers looking into the benefits of using pods in their developments. They can help reduce programme, meaning that properties are occupied sooner and return on investment is gained earlier too. This can save on construction loan interest, giving a more rapid return to investors.